1967-1971
From ’67 to ’71 I was attending the University of Arizona toward a BS in Electrical Engineering. My interest in ham radio had faded, replaced by a fascination with sound and audio engineering, and somehow I found time to work several side jobs while still in college.
KXEW-AM had landed an FCC license to add an FM signal. They promoted me to Chief Engineer and had me supervise the purchase and installation of a 5 kW FM transmitter and a second broadcasting studio. This was great fun for an 18-year-old nerd! To avoid the expense of adding a second full-time DJ, we installed one of the early “automated” radio studios, with reel-to-reel tape recorders and robotic drums of tape cartridges. With PCs not yet developed, this ran on banks of telephone stepping relays and was programmed with a telephone dial. You can probably guess that this Rube Goldberg contraption did not survive for long.
It was around this time that ICs (integrated circuits, or “silicon chips” to the layman) became available to hobbyists and experimenters. I wanted to try building a circuit with both analog and digital ICs, so I designed and built a compact automated studio console for KXEW’s remote broadcasts. This was my first “professional” electronic project. Operational amplifier ICs served to mix audio from a microphone, two turntables, and two cassette playback decks. Digital logic ICs automatically started and stopped the turntables and decks when you pushed a single button.
To protect the setup in mobile use, I also built a custom, padded “roadie” case from plywood. Now I can see that this project was the precursor of two of my lifelong hobbies, electronics and woodworking.
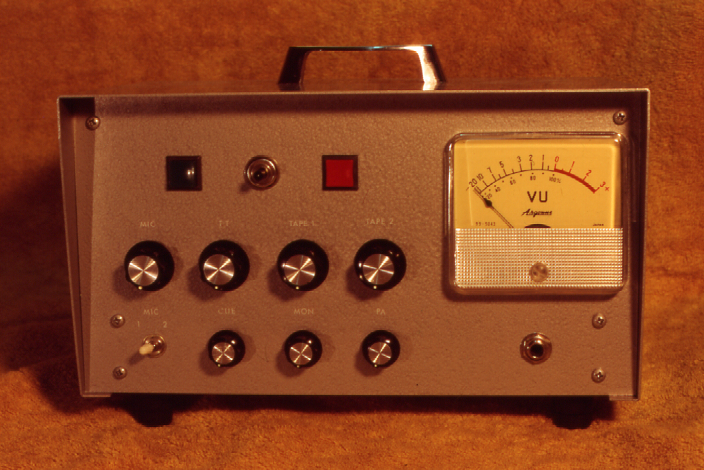
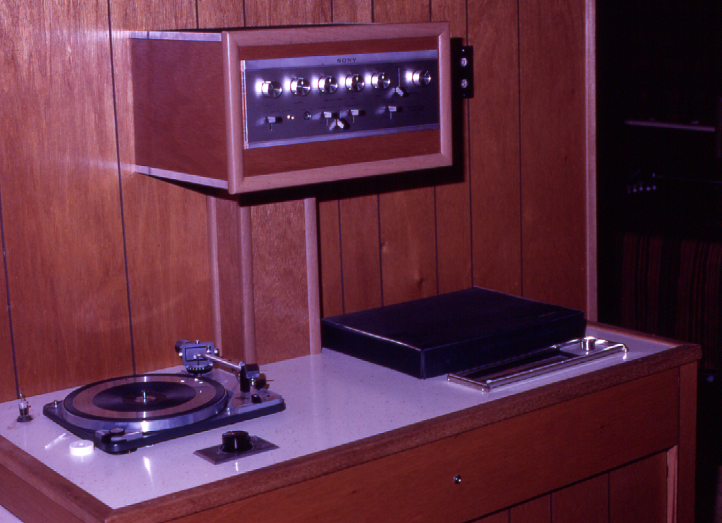
Around this time, I learned that a new recording studio had opened up in Tucson. I dropped in on a whim to see if they had any openings. Forster Cayce, owner of Copper State Recording Studios, was always looking for technical help, so he graciously gave me the grand tour. His studio had a brush with greatness, doing early sessions with Alyce Cooper and Linda Ronstadt, but I never met anyone famous. I mainly cleaned and aligned the massive Ampex multitrack recorders, and occasionally helped with roadie duties. But I eagerly absorbed lots of new knowledge about sound and recording. And I took advantage of their commercial discounts to customize my home stereo with massive studio-quality Altec speakers. As I entered my final year of college, I thought I was headed for a career in audio engineering. I was wrong.